Detrás de escena de la creación de ACC Gigafactory IS
hace 2 años
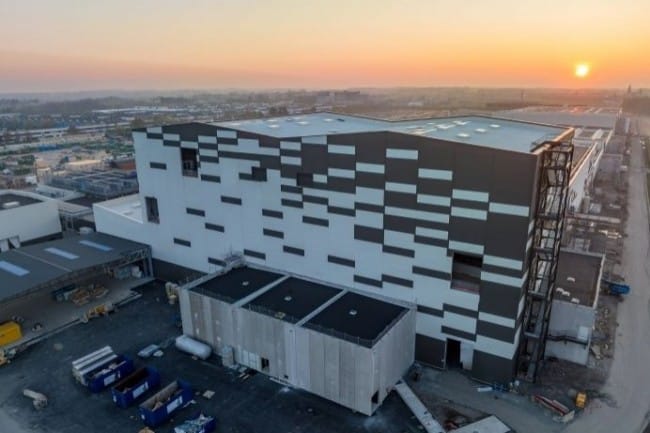
En Hauts de France, ha surgido la primera gigafábrica francesa de baterías para automóviles. Para apoyar esta nueva actividad, DSI de ACC, líder industrial de este proyecto, construyó un sistema de información en un tiempo récord. Informes.
Un transatlántico de más de 600 metros de largo colocado en el antiguo emplazamiento de la Française de Mécanique, a caballo entre las localidades de Billy-Berclau y Douvrin, entre Lens y Lille. La primera Gigafactory en Francia sigue siendo como una colmena. Casi mil trabajadores, incluido un gran número de coreanos y chinos que entregan la mayoría de las máquinas en el corazón del complejo proceso de producción de baterías industriales, todavía están ocupados finalizando la fábrica, que debe entregar sus primeros módulos de batería en Stellantis el próximo noviembre. Un calendario acotado que empuja a ACC (Automotive Cells Company), la industrial detrás de este proyecto y que cuenta con el apoyo del Estado y de los principales accionistas (TotalEnergies, Stellantis y Mercedes-Benz), a comenzar a tomar el control del futuro dispositivo de producción. Los primeros 300 empleados de la fábrica de Billy-Berclau Douvrin (o BBD) ya están trabajando duro. Se espera que el sitio alcance los 1.200 empleados en 2025, según los planes de ACC.
En el lado de TI, François Carrot, el DSI, debe enfrentar limitaciones similares: entregar rápidamente un sistema de información mínimo, mientras construye el del mañana, cuando la empresa tendrá 3 gigafábricas (Billy-Berclau-Douvrin, Kaiserslautern en Alemania y Termoli, Italia ) y dará empleo a más de 10.000 personas. "Partimos de una página en blanco, pero pensando en grande", dice el CIO, reclutado en noviembre de 2020 después de una carrera de alrededor de treinta años en el automóvil. Uno de los desafíos es apoyar el escalamiento del joven industrial - ACC nació a principios de 2020 -, primero con el nacimiento en 2021 del centro de I+D en Brujas (cerca de Burdeos), a partir del cual se desarrollaron los primeros módulos, luego la creación de la planta piloto de Nersac, en 2022. Y ahora, Billy-Berclau-Douvrin, en una escala completamente diferente. El primer bloque que se está finalizando -la planta debería llegar a tener 3- tiene una capacidad de producción de 13,4 GWh 24/7, los 365 días del año. ¡Suficiente para equipar de 100 000 a 200 000 vehículos!
“No hay modelo para replicar”
“A nivel de TI, comenzar desde una página en blanco es obviamente una oportunidad única, continúa DSI. Excepto que no había ningún modelo que pudiéramos replicar. Y tuvimos que construir muy rápido el sistema de información para cubrir las necesidades esenciales de ACC, y sobre todo construirlo al mismo tiempo que se construía la empresa, su centro de I+D, su organización, sus fábricas”. Si bien el departamento de TI puede depender de los accionistas de la empresa por un tiempo para ciertas funciones multifuncionales (contabilidad y nómina), la mayor parte de su hoja de ruta surge de las expectativas del director general, Yann Vincent.
François Carrot, DSI de ACC (a la izquierda) y Lionel Taisne, director de TI de la gigafábrica Billy-Berclau-Douvrin. Detrás de ellos, el pasillo principal de la fábrica, de más de 600 metros de longitud. (Imagen RF)
En la parte superior de la lista, el deseo de ponerse al día con los fabricantes asiáticos. “De ahí una exigencia de rendimiento, control de los costes de producción y reducción de la chatarra, en particular la tasa de módulos de calidad insuficiente (en jerga, chatarra, nota del editor) que deben ser reciclados. Desde el principio, nos pidió que usáramos los datos tanto como fuera posible para controlar estos parámetros”, continúa François Carrot. ACC tradujo su ambición sobre los datos creando una entidad dedicada a la valorización de datos, una entidad gestionada por un CDO (Chief Data Officer).
Para el inicio de la producción, ACC planea medir la calidad en cada paso de un proceso de fabricación de nueve pasos. "Si no entramos en detalles, no avanzaremos en el desecho (la tasa de celdas que fallan, nota del editor)", dice el DSI. (Foto: CCA)
Otro elemento clave señalado por el gerente, y muy sensible en las elecciones de François Carrot y sus equipos: la ciberseguridad. En particular, la capacidad de proteger el aparato de producción de amenazas externas. “¡Porque es una de las formas más simples de hacernos quedar atrás en la competencia global que está comenzando! “, señala el DSI. Por ahora, dentro de la gigafábrica BBD aún en construcción, las máquinas siguen siendo propiedad de sus fabricantes asiáticos. "Tan pronto como finalice la transferencia de propiedad, realizaremos una auditoría de seguridad para rastrear cualquier falla y otro acceso remoto", explica Lionel Taisne, gerente de TI de la primera planta de ACC.
Trazabilidad: a nivel alimentario y farmacéutico
El consejero delegado marca otras dos prioridades en la hoja de ruta del departamento de TI: el cumplimiento de la política de RSC del grupo -sin olvidar la contribución de las TI al control de las emisiones de la compañía- y la trazabilidad en toda la cadena. de fabricación, debido a la peligrosidad de los productos manipulados. “Los requisitos de responsabilidad social y ambiental son esenciales. Desde cada celda al final de la cadena hay que poder volver a la tira (una lámina de aluminio o cobre donde se recubren las tintas, nota del editor) ya las materias primas, litio y manganeso. Este vínculo genealógico está al nivel de lo que se encuentra en la industria alimentaria o farmacia”, dice el DSI.
Estos gabinetes gigantes, instalados al final de la cadena, se utilizan para probar las celdas, mediante ciclos de carga y descarga. ACC tiene la intención de utilizar el aprendizaje automático para predecir la curva de descarga y así escuchar este proceso que se extiende a lo largo de varios días. (Foto: RF)
Esta exigente hoja de ruta, sumada al apretado cronograma para aumentar la actividad, empuja a la DSI a trabajar con un doble foco. "Ambos debemos entregar sistemas a corto plazo, porque las expectativas son altas, mientras nos preparamos para cumplir las ambiciones mostradas en dos o tres años", resume François Carrot. Hoy, compuesto por unas cuarenta personas a nivel central (los equipos de TI también están desplegados en las fábricas, que conservan una autonomía considerable en términos de TI, ver recuadro), el TI de ACC se divide en seis grupos, lo que refleja los problemas clave que enfrenta la empresa. : infraestructura y ciberseguridad; ERP; ingeniería, industrialización y calidad (principalmente en torno a PLM); funciones multifuncionales (como recursos humanos); gestión de datos; y, finalmente, fabricación, en torno al MES (donde se seleccionó Aveva de Schneider Electric). “Nuestro método de trabajo consiste en trabajar deliberadamente en silos, con pocas interfaces, para que cada uno pueda avanzar a su propio ritmo”, explica el CIO. Pero nos aseguramos de definir nuestros datos de referencia para crear interfaces más tarde. »
Dominio de la logística: avanzando paso a paso
Para avanzar rápidamente, François Carrot emitió lo que presenta, con una sonrisa, como un ukase: "tomar solo sistemas listos para usar, sin desarrollo específico". Un ejemplo emblemático de esta voluntad de mantenerse dentro del estándar para avanzar con rapidez: la implantación de QAD ERP en cuatro meses, para finanzas y compras indirectas. Instalado por primera vez en las instalaciones, el paquete de software migró desde entonces a una nube para respaldar la estrategia del editor. "A pedido nuestro, este entorno se instaló en OVH, en lugar de IBM, que es el host habitual de QAD", especifica François Carrot. El ERP también se ha extendido a la logística y las compras directas, un problema importante dado el costo de los flujos de materiales que manejará ACC. “Avanzaremos por etapas. Por ahora, estos procesos están soportados por nuestro ERP. Pero, cuando sea necesario ir más allá en la gestión del transporte o las previsiones -a partir de 2024-, nos plantearemos sistemas complementarios”, apunta el DSI.
Del lado del primer edificio de la gigafábrica, se demolieron antiguos edificios de la Française de Mécanique y se niveló el suelo. Es aquí donde se construirá la segunda fase, prevista para finales de 2025 o principios de 2026. (Foto: RF)
Para estos últimos, otro tema cobra aún más complejidad: el MES. “Porque tenemos que construir el sistema mientras mejoramos nuestro control del proceso de fabricación”. El especialista interno en el tema acaba de ser contratado. Esta cuestión del control del proceso industrial también es central en la explotación de los datos: también allí, el DSI debe recuperar los datos resultantes de sus procesos de fabricación al tiempo que entrega los primeros análisis, esenciales para el control de la calidad. El centro de I+D y la planta piloto de Nersac han permitido recoger los primeros datos de los equipos. “Nuestro equipo de datos lo utilizó para crear las primeras aplicaciones relacionadas con la genealogía de productos y para ofrecer los primeros paneles. También se ha desarrollado una aplicación para tabletas para que los operadores puedan ingresar información”, señala el DSI. "Para la recuperación de datos de máquinas, aprendimos sobre el agua", abunda Lionel Taisne.
Datos a escala de una gigafábrica
Pero la gigafábrica de Hauts-de-France pone el listón aún más alto. Tanto en términos de escala (por ejemplo, solo una máquina apiladora está presente en la planta piloto, donde se implementarán 46 en BBD), como en términos de diversidad de equipos implementados. “Estamos ante un gran trabajo de dominio de datos. Cada OEM puede proporcionarnos una serie de variables. Aparte de que estos no necesariamente están traducidos del chino o del coreano, hay que determinar a qué corresponden y su utilidad real”, resume Lionel Taisne. Por lo tanto, los equipos de ACC están en el proceso de construir tablas de intercambio entre los formatos de origen y los formatos de destino, tablas que el fabricante planea integrar en sus futuras licitaciones, que se lanzarán para lo que la compañía llama su Wave 2 (es decir, el segundo tramo de BBD, el primero de Kaiserslautern y dos tramos en Termoli). “Por el momento, todavía estamos muy lejos del mundo onírico del OPC UA* plug & play”, desliza François Carrot.
*: OPC UA (Open Connectivity - Unified Architecture) es un estándar de intercambio de datos que facilita la interoperabilidad de los sistemas industriales. El estándar es mantenido por la Fundación OPC, un consorcio de la industria que se especializa en estándares de automatización.
Si quieres conocer otros artículos parecidos a Detrás de escena de la creación de ACC Gigafactory IS puedes visitar la categoría Otros.
Otras noticias que te pueden interesar